Captain 3D #3DPrinting
Thanks for sending us a link to your impressive project Victor! This stop motion film has been in the works for years and uses 3D printing technology! Interview with director Victor Haegelin via Stash Media
Join irrepressible French director Victor Haegelin as he reveals the stop-motion process and unlikely origin behind “Captain 3D,” his superhero adventure starring a girl, a monster, and a guy with no superpowers at all.
Victor Haegelin: “The project started when I was pitching on a commercial for a smartphone brand that wanted to push the quality of their camera so I suggested shooting a film with two smartphones stuck together in order to make 3D a relief stop-motion animation.
“So I wrote a story and Captain 3D was born. Then the brand decided not to make the film and I had that screenplay ready that I really really want to make.
“After a year of sleeping, we decided to find money to make that film. Gizem and Nathalie, the two producers were wonderful and they believed we could do it.
“It was very challenging because we wanted to shoot it in relief, with 3D-printed technology (for the faces) and I wanted it to be Hollywoodian.
“We built the puppets in Brittany at JPL Studio. We built the set and props and shot at Asniere in the Manuel Cam Studio. Then post-production (cleaning,3D, grading) was done at Royal Post in Paris.”
Learn more and check out the Captain 3D short below!
Study Examines Compressive Behavior of 3D Printed Lattice Structures
Lattice structures are frequently found in additive manufacturing, as their complex forms are easy to make using 3D printing. The technology also makes it possible to construct them from multiple materials. Because of their high specific strength and stiffness, lattice structures are often used in the aerospace, defense and automotive industries. In a paper entitled “Compressive Behavior of Strut Reinforced Kagome Structures Fabricated by Fused Deposition Modeling,” a group of researchers investigates the compressive performance of modified Kagome unit cells.
Kagome is a type of lattice structure defined by the researchers as “a stretch dominated 3D truss structure derived from the design pattern of a woven basket.” A modified version of Kagome structure is strut reinforced Kagome (SRK), which has been shown to have better compressive properties than standard Kagome. For the study, the researchers used ABS to 3D print SRK structures.
“Uniaxial compression tests were carried out in Shimadzu Universal Testing Machine using 10 kN load-cell, and compression load was applied under displacement control at a rate of 0.1 mm/min,” the researchers explain. “Video extensometer TRViewX was used to measure the accurate displacement between the faceplates. The engineering stress-strain data are obtained from the measured force (F) and displacement (h). The stress was calculated by dividing the force by the effective area which is obtained in terms of truss length ( l = 2c) 2 3 c2, whereas the strain is obtained by dividing the displacement by the core height.”
The tests showed that the peak strength and effective modulus increase with the decrease in the slenderness ratio. In addition, SRK structures show different failure behavior with the change in the slenderness ratio.
“The core with lowest relative density (d =2.4 mm, h = 35mm) shows the failure within the linear elastic regime,” the researchers continue. “As the slenderness ratio is very high, the struts failed by elastic buckling without any yielding. With the increase in the relative density (d =2.4 mm, h = 25 mm), there is some plastic deformation before reaching the peak strength as shown in the Figure 2. With further increase in relative density (d = 3 mm, h = 25 mm), we can see the significant plastic nonlinearity before reaching the peak strength. The stress gradually decreases with the increase in the strain.”
The vertical struts in all the samples started to deform after substantial compression. Plastic bending of the vertical strut results in the distortion of the upper and lower part of the SRK, leading to the deformation of the slanted struts. Further compression leads to the formation of surface cracks on the tensile side of the strut. With further loading, the cracks open, leading to the bending of the structure, additional cracks on all sides, and eventual softening and collapse of the structure.
“The anisotropic material behavior and the porous nature of FDM printed structure have led to the discrepancies in the numerical and experimental results,” the researchers conclude. “The performance of SRK unit structure can be further improved by the variation in diameter of the slanted and vertical struts to optimize it for a given density.”
Authors of the paper include Rinoj Gautam, Sridhar Idapalapati, and Estella Siew Lee Koh.
Discuss this and other 3D printing topics at 3DPrintBoard.com or share your thoughts below.
New Products 09/08/2018 Featuring Adafruit #CRICKIT for #microbit! @adafruit #adafruit
Browse through all that’s new here!
NEW PRODUCTS THIS WEEK
Girl CEO by Ronnie Cohen & Katherine Ellison:
“That girl thinks she’s the queen of the neighborhood
She’s got the hottest trike in town
That girl she holds her head up so high
I think I want to be her best friend, yeah
Rebel girl, rebel girl
Rebel girl, you are the queen of my world”
Girl CEO is an illustrated collection to inspire and motivate rebel girls, young entrepreneurs, and other trailblazing tweens and teens with success stories and practical advice from leading women entrepreneurs (including *drumroll* Limor “Ladyada” Fried!). Read more!
2600: The Hacker Quarterly – Winter 2017-2018: 2600: The Hacker Quarterly is an American quarterly journal specializing in issues surrounding hacking, telephone switching systems, internet protocols, telecommunications in general, the politics around high technology, and its impact on society.
With origins in the phreaking community and late 20th century counterculture, 2600 and its associated conference transitioned to coverage of modern hacker culture, and the magazine has become a platform for speaking out against increased digital surveillance and advocacy of personal and digital freedoms. See more!
USB C to Micro B Cable – 3 ft 1 meter: As technology changes and adapts, so does Adafruit! Rather than the regular USB A, this cable has USB C to Micro B plugs!
USB C is the latest industry-standard connector for transmitting data and power. Like Lightning and MagSafe cables, USB C has no up or down orientation. And who among us has inserted USB correctly the first time? Works great with any computer that has a USB C port, and will let you attach any of our dev boards with classic Micro B connectors (which is, like, 95% of them) Read more!
USB C to Micro B Cable – 1 ft 0.3 meter: As technology changes and adapts, so does Adafruit! Rather than the regular USB A, this cable has USB C to Micro B plugs! See more!
Rotating Door Lock DC Motor: Adding to our collection of somewhat specialized motors, this Rotating Door Lock Motor is a DC Gearbox motor with a little pocket that is intended for a door look mechanism. The motor only turns 90 degrees clockwise or counter-clockwise and will stall (but not strip) if you try to keep running it past the angle.
It’s geared down so it has high torque, but that also makes it slow – it is about 5 seconds for it to rotate ‘closed’ or ‘open’. That said, we like that you can power it from approximately 5V so its easy to hook up to your microcontroller or computer using Crickit and Arduino, CircuitPython or MakeCode. See more!
Monoprice Inventor II 3D Printer with Touchscreen and WiFi: The Monoprice Inventor II 3D Printer Touchscreen with WiFi is a perfect entry-level 3D printer with small footprint and reliable performance. It comes equipped with WiFi so you don’t need a cable tether and a lovely 3.5″ color touchscreen for settings & feedback. The chassis housing is enclosed to keep your prints safe, and if you wanted to upgrade this printer for a heated bed, you’ll be able to keep the build volume warm. This printer has an automatic sensor door that will shut off any current printing job in progress if/when the door is opened. The printer keeps noise to a minimum as well as making it super easy to set up prints right out of the box. See more!
Adaptive Design’s Morse Code for GBoard Hardware Interface Pack: At the time of its invention Morse code definitively changed the way we communicate. Historically it’s been used in nautical navigation to aviation to radio, but its easy to learn and the universal nature makes it a great data entry method for folks who use Assistive Technology!
GBoard is an alternate keyboard for Android devices that lets you type using Morse code. It then converts those dots and dashes into letters and numbers, letting someone control a tablet or phone with only two buttons. The Morse Code for GBoard Interface Starter Pack will help you build a simple input device for GBoard that doesn’t require soldering or elaborate construction techniques. See more!
NeoPixel RGB Neon-like LED Flex Strip with Silicone Tube – 1 meter: No joke, we have been looking for this exact product for over 5 years, and we’ve finally got the perfect one in stock! You love NeoPixels, and you love silicone diffusion? Peep this NeoPixel RGB Neon-like LED Flex Strip with Silicone Tubing! OK its a bit of a mouthful but check out the beautiful pics! It looks a lot like neon, but without the need for expensive transformers, glass tubing, inert gasses, or a Las Vegas casino license. They look incredible, are super easy to use, and are a great way to make your projects light up! See more!
Adafruit CRICKIT for micro:bit: Sometimes we wonder if robotics engineers ever watch movies. If they did, they’d know that making robots into slaves always ends up in a robot rebellion. Why even go down that path? Here at Adafruit, we believe in making robots our friends!
So if you find yourself wanting a companion, consider the robot. They’re fun to program, and you can get creative with decorations.
With that in mind, we designed Crickit – That’s our Creative Robotics & Interactive Construction Kit. It’s an add-on to the BBC’s micro:bit that lets you #MakeRobotFriend using MakeCode or Arduino. See more!
New Products 9/5/2018 Featuring Adafruit #CRICKIT for #microbit!
Want to get this info beamed straight into your inbox?
New nEw NEWs From Adafruit is an email newsletter sent once a week to subscribers only.
It features new products, special offers, exciting original content, and more.
Sign-up for the Adafruit weekly Newsletter here: https://www.adafruit.com/newsletter
3D Printing Mythbusting with Braille Skateboarding
A Generatively Designed Skateboard from Fusion 360 and Shapeways
Industrial Designer Paul Sohi is obsessed with 3D printing. He’s made it his life’s work to make it accessible to more people – a mission we share. His earlier efforts include developing the world’s first fully additively manufactured prosthetic used at the Paralympic Games. More recently, he has been evangelizing for Fusion 360 at Autodesk.
A skateboard was ideal for Paul’s latest project. He wanted to design a fun, common item to debunk many 3D printing myths still common today by proving that 3D-printed products are end-use ready, durable and not just for prototyping. Just as important, Paul wanted to prove that you don’t have to buy a 3D printer. He explains, “The number one misperception I hear from designers is that they have to buy a 3D printer. I want to show that Shapeways’ services are part of the Fusion 360 workflow.”
Paul used Fusion 360 Generative Design to make the skateboard trucks (the metal T-shaped pieces that mount onto the underside of the skateboard) durable while also minimizing materials to cut costs. He sent the files to Shapeways, and we delivered the trucks in two materials: titanium and aluminum, both manufactured using additive manufacturing. Paul constructed the entire skateboard from board to wheels to trucks, and headed to California.
Braille Skateboarding was founded by Aaron Kyro and creates videos to help spread the joy of skateboarding. They joined the project to see if Paul’s skateboard trucks could enhance Braille’s tricks. We wanted to show the skate trucks’ functionality all while capturing some great runs on a board made possible with 3D printing and generative design. More than just a 3D printing stunt, our team wanted to focus on making skateboarding an even better experience with increased durability and mobility. We succeeded – Paul estimates the trucks are 35% lighter and twice as durable versus comparable skateboard trucks.
We captured videos of Braille’s tricks and details on how the skate trucks were made. Special thank-you to Paul, Braille, and Autodesk for making this so much fun. Shapeways loved helping to bring this idea to life.
The post 3D Printing Mythbusting with Braille Skateboarding appeared first on Shapeways Magazine.
Researchers Develop Electrically Conductive PEEK Filaments
A joint research project has just revealed the capabilities of electrically conductive PEEK filament for FFF/FDM. The researchers produced the material by adding carbon nanotubes and graphite nanoplates, incorporating carbon-based electrical conductivity as opposed to metal. While nanotubes allow for a range of material properties in filament, this is the first time researchers used their […]
The post Researchers Develop Electrically Conductive PEEK Filaments appeared first on 3D Printing.
3D Printing News Briefs: September 8, 2018
We’re starting out with a lot of business news in today’s 3D Printing News Briefs, and then finishing up with something cool (pun intended) to get you through the weekend. Link3D launched its new Production Planning System for AM workflows, Carbon has a new medical-grade material, and there’s new 3D printed footwear on Kickstarter. Several US sleep experts have joined the Oventus medical advisory board, HP’s MJF technology is being used to make assemblies, and GKN Aerospace is improving its production times with Stratasys technology. Bradley Systems has suggested using its Yellow Magic 7 to clean your SLA 3D printers. Finally, a mechanical engineer and 3D printing blogger has created a retro air cooler.
Link3D Launches Production Planning System
New York City-based Link3D, which offers a centralized software platform for the industrial 3D printing workflow over external or internal additive manufacturing, has just announced the availability of its Production Planning System (PPS) and Advanced Build Simulation. PPS, an AM scheduling solution meant to enhance the company’s software for shop managers and application engineers, can further optimize AM workflows, helping 3D printers to run more efficiently and automate various tasks, like tracing and tracking a build’s genealogy, planning out each step of a build, managing scheduling, facility capacity, and production dispatching, and forecasting accurate production lead times.
“Our comprehensive predictive models are made to forecast AM production and costing outputs by accounting for labor, hardware model, AM technology, post-processing and including material science variables like specific gravity and viscosity. Link3D PPS utilizes machine learning algorithms to make recommendations for placing work orders on the correct machines based on machine availability to achieve real-time distributed manufacturing,” said Shane Fox, the CEO and Co-Founder of Link3D.
Link3D PPS will use blockchain technology to trace and track all of the data logged and generated, so organizations can validate and certify their production processes.
Carbon Introduces New Medical-Grade Material
This week, Carbon announced the launch of its first medical-grade 3D printing material, a two-part, white polymer resin called Medical Polyurethane 100 (MPU 100). The material is made for drug- and skin-contact devices, medical system components, single-use medical device, and surgical instrument applications. The material is sterilizable, biocompatible and has good mechanical strength. MPU 100 has good abrasion resistance, is compatible with common disinfectants, and works with the company’s Digital Light Synthesis (DLS) technology to produce rigid, isotropic plastic parts.
“The life sciences and medical device industries show enormous promise for using 3D printing for production at scale, and we will continue to prioritize the development of next-generation materials in this segment,” said Jason Rolland, Vice President of Materials at Carbon.
Carbon is offering MPU 100 in 800 ML cartridges to its customers in Europe, the US, and Canada. You can learn more about the new medical-grade material at Carbon’s booth #431505 in the West Hall at IMTS 2018 next week.
Unis Brands Starts 3D Printed Footwear Kickstarter
Earlier this week, Unis Brands began a Kickstarter campaign for its line of user-customizable, 3D printed footwear. The line includes two different styles of sandals: the U-Straps and the U-Slides, both of which will be available, in limited quantities, to early campaign backers for just $75 and $100, as opposed to the regular retail price of $140. The 3D printed U-Straps and U-Slides offer custom sizing, as customers provide the exact length and width measurements of each foot. The sandals are made with flexible 3D printing filament for a comfortable fit, and each one has five components, including the logo, buttons, cushion, upper, and midsole, that can be customized with different patterns and colors.
Unis said, “After getting my start in footwear by taking popular sneakers apart, customizing them, putting them back together and then selling them on eBay, I’m excited to announce my first line of sandals on Kickstarter. With five different user-customizable areas, and with individually 3D-printed shoes based on each customer’s exact foot measurements, we are creating footwear that is truly one-of-a-kind.”
All of the company’s recyclable shoes are made in the US on 3D printers designed and built by CEO and founder Nicholas Unis.
US Sleep Experts Join Oventus Medical Advisory Board
Brisbane medical device company Oventus, known for its FDA-approved, 3D printed sleep apnea device, recently announced that it had appointed a Medical Technology Advisory Board (MTAB) of international sleep experts. The board will assist and guide the company on the development and commercialization of its Sleep Treatment Platform. The MTAB, a US-based consultative advisory body, will report to Oventus CEO Dr. Chris Hart, and provide guidance and input into the company’s clinical, developmental, and commercial strategy, which is currently focused on introducing its products to the US.
The following top sleep physicians and advisors in the US have been appointed to the Oventus MTAB for a three year term, which is renewable by mutual agreement:
- Lee A. Surkin, MD, FAASM
- Richard K. Bogan, MD, FCCP, FAASM
- Jerry Kram, MD, FAASM
- Mark Hickey, MD, FAASM
- Mark A. Rasmus, MD, FAASM
- Daniel B. Brown, Esq
- Myra G. Brown
Aerosport Modeling & Design Making Assemblies with HP’s MJF Technology
Ohio-based 3D printing service bureau Aerosport Modeling and Design, which has been producing high-quality prototypes, working models, machined parts, and appearance models since 1996, adopted HP’s Multi Jet Fusion (MJF) technology nearly a year ago.
The company uses MJF 3D printing to fabricate assemblies, such as a Butterfly Valve one made of PA 12 Nylon. The original assembly came in 30 pieces and took half an hour to assemble. But by using HP’s 3D printing technology to make it, the total number of pieces was reduced to just four, with only three minutes of assembly. This helped Aerosport lower its production costs by 70%, and its production time by an astonishing 90%.
GKN Aerospace Improving Production Times with Stratasys 3D Printing
This week, Stratasys announced that GKN Aerospace, which serves over 90% of the world’s aircraft and engine manufacturers, is removing design constraints and improving production times for many tooling applications after integrating 3D printing at its Filton manufacturing site. In an effort to lower lead times for production-line tools and create complex parts that can’t be completed with traditional manufacturing, GKN Aerospace invested in a Stratasys F900 Production 3D printer. This decision helped the company achieve “unprecedented levels of design freedom,” as well as a 40% decrease in material waste; production has also gone from several weeks to only a few hours.
Tim Hope, Additive Manufacturing Center Manager at GKN Aerospace, said, “Since integrating the F900, we have dramatically reduced production-line downtime for certain teams and are enjoying a newfound freedom to design complex tools.
“We can now cost-effectively produce tools for our operators within three hours. This saves critical production time, and by printing in engineering-grade thermoplastics, we can produce 3D printed tools with repeatable, predictable quality every time. All while matching the quality of a traditionally-produced tool, and reducing the costs and concessions compared to equivalent metallic tooling.”
Bradley Systems Wants You to Clean Your SLA 3D Printer with Yellow Magic 7
If you’ve got an SLA 3D printer that needs a good cleaning, Bradley Systems, Inc. wants you to consider using its Yellow Magic 7 (YM7) cleaner, as opposed to Isopropyl Alcohol (IPA), which is also called isopropanol and dimethyl carbinol. The company first heard about people using its cleaner, which was originally formulated as a flexo UV ink and varnish cleaner for printing human and pet food packaging, to clean parts for SLA 3D printers on a Formlabs forum, and has since started offering 1 gallon jugs of YM7 on Amazon…and this decision is garnering it some pretty positive reviews.
“Until now, IPA has been the go-to cleaner for this application because it gets the job done. The downside is that IPA is a flammable chemical compound with a strong odor. This means you’ve got to make sure you’re wearing personal protective equipment (PPE) and storing it properly so you don’t accidentally blow yourself up. As for the smell… well there’s not much you can do there,” the company wrote in a blog post.
YM7, unlike IPA, is biodegradable, non-toxic, and has little odor. It’s not a fire hazard, as it’s water based, and it also performs well in an ultrasonic cleaner. It’s also versatile enough to clean a multitude of different 3D printer parts and accessories, like rollers and rubber pads.
“So, what we’re seeing so far is that you can still get the job done using Yellow Magic 7 without the stink or the potential of blowing up your co-workers or family. Which is nice.”
Mechanical Engineer Builds 3D Printed Retro Air Conditioner
While 3D printing is a relatively modern technology, it can be fun to use it to recreate your favorite retro items from the past, like arcade games, original Apple computers, FM radios, and television sets…even scuba helmets! A mechanical engineer named Juan, who owns a YouTube channel and blog titled Govaju 3D Printing, has worked in the 3D printing world for eight years, 3D printing is not only his work, but also his hobby and passion. Recently, Juan decided to get back to the past by creating a 3D printed retro item of his own.
“I recently created this video of a project that I’ve been working on for a few months, it’s a retro air conditioner,” Juan told 3DPrint.com. “It is printed 100% in 3D with the lulzbot taz 6 and with wood filament and PLA.”
Take a look at the video to see the project come together!
Discuss these stories and other 3D printing topics at 3DPrintBoard.com or share your thoughts below.
Monitoring the Laser Powder Bed Fusion 3D Printing Process with Spectroscopy to Detect Defects
Laser powder bed fusion 3D printing, one of the most well-established processes for producing metal parts, uses a powder bed of material to build a part layer by layer. The part is formed when energy is put into the powder to fuse it together, which can achieve parts with high resolution at high productivity.
Unfortunately, a lot of things can go wrong and cause defects in metal parts made with powder fed fusion 3D printing, such as cracking, root concavity, residual stress, porosity, balling, delamination, microstructural impurities, and surface defects. 3D printed metal parts with defects can cause safety issues and compromised functionality, and while some issues can be detected and fixed during post-processing, others can’t, which results in part failure. In order to detect and correct defects before it’s too late, we need to keep studying the source of these defects.
Andrew Drieling from Wright State University in Ohio recently published a paper, titled “In Situ Defect Detection Using Three Color Spectroscopy in Laser Powder Bed Additive Manufacturing,” about using spectroscopy to monitor 3D printing for defects.
The abstract reads, “Additive Manufacturing (AM) provides a way to create parts that would be extremely difficult or impossible with conventional manufacturing processes. However, AM also introduces defects, which are detrimental to the mechanical performance. These defects are potentially unknown until post-processing inspection and testing, wasting time and resources on an unusable part or initiating unexpected failure. Historically, spectroscopy has successfully been used for in situ monitoring of laser welding, using changing parameters in the generated plume to predict defects. In situ monitoring using a visible spectrometer for fabrication of Alloy 718 on a test bed laser powder bed fusion system is performed. AM defects, such as keyhole porosity and unfused powder, are detected in the sensor output and a physics-based modeling approach is used to predict defect occurrence. Spectroscopy can provide near real-time monitoring, allowing defects to be predicted, and potentially corrected before the completion of the part, saving time and resources.”
In his paper, Drieling explained that spectroscopy is the study of matter’s absorption and emission of light and other radiation as it relates “to the dependence of these processes on the wavelength of the radiation.” It actually measures the interaction between matter and photons.
There has been previous research completed regarding the use of spectroscopy for defect detection and closed loop control of laser welding processes – it can be used to provide real-time monitoring of the 3D printing process, which can save time, money, and resources by making it possible to detect any defects early enough to correct them.
“If defect detection is important in laser welding, where it is only a single pass and the surface of the entire weld can be seen, then it is even more important in laser powder bed fusion where most of the welds are hidden by the top surface,” Drieling wrote. “The defects found in laser powder bed fusion are determinately to part performance and current methods to detect defects cannot be employed until fabrication of the part is complete, even then, not all defects can found by nondestructive methods. With current methods, the part must be completely fabricated, then if unacceptable defects are detected, all the time and resources put into that part have been wasted. If the defects go undetected, then they can initiate unexpected failure, leading to potentially dangerous situations.”
Drieling used a custom built laser powder bed fusion 3D printer from Universal Technology Corporation for his research and recorded data with a spectrometer, a high-speed camera, a profilometer, and visible and thermal cameras as well. He ran 15 individual tests, while varying the power and speed parameters, to see if this had any effect on the spectroscopy data.
“Once the experiment was complete, the beads were examined under a microscope and accessed for quality,” Drieling wrote. “The top set of five were run at 500 mm/s, the middle at 1000 mm/s and the bottom at 1500 mm/s. Within each group, the top bead was run at 450 watts, running down through the power levels to 150 watts for the bottom bead.”
Three features were looked at for possible future experiments while the beads were being examined: keyholing, balling, and highest quality of bead.
“Keyholing was most prominent in the 500 mm/s, 450 watt “High Power” bead,” explained Drieling. “The 1500 mm/s, 375 watt “Low Power” bead was chosen for balling features. It should be noted that the 1500 mm/s, 430 watt bead exhibited worse balling behavior, however it wasn’t able to maintain a continuous bead, therefore it wasn’t chosen. The 1000 mm/s, 225 watt “Nominal” bead was chosen for having the highest observable quality in terms of bead width and consistency. These three beads were further examined using the spectroscopy data.”
By varying the processing parameters, Drieling saw a range of defects in the produced beads; after analyzing the spectroscopy data, he saw that the intensity values varied for the defects and that the intensity data is not only affected by the energy input, “as two beads studied had similar energy inputs and different intensity readings.”
“All these results show that closed loop control of laser powder bed fusion is possible with spectroscopy,” Drieling concluded.
In the future, Drieling plans to expand the build to larger geometries, like cubes.
Discuss this research and other 3D printing topics at 3DPrintBoard.com or share your thoughts below.
Assessing the Potential for 3D Printed Equipment in Cleanrooms
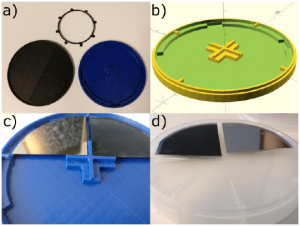
a) Wafer box for four 100 mm wafer quarters 3-D printed out of PLA including top (black), bottom (blue) and holder (black ring). b) Open SCAD model of the customizable single wafer box. c) Wafer quarters stored securely in the 3-D printed box. d) Wafer quarters free to move in a commercial single wafer box.
3D printing has been used by scientists to save money on lab equipment, which is typically quite expensive. Things get a bit complicated, however, when it comes to equipment that is used in clean rooms. There are strict limitations on the types of materials and items that are allowed in cleanrooms, so a good deal of study and experimentation must be done before clearing a new item or material for use. That is the purpose of a study entitled “Compatibility of 3-D Printed Devices in Cleanroom Environments for Semiconductor Processing.”
“As the dimensions of typical semiconductor devices are in the micrometer range, it is essential to fabricate those components in an environment, where the level of contaminants (e.g. dust particles and organic compounds) is accurately controlled,” the researchers explain. “In cleanrooms, the level of contamination is specified by the number of particles per cubic meter at specified particle sizes by the international ISO (the International Organization for Standardization) standards.”
To meet these requirements, air flowing into the cleanroom is filtered and recirculated through HEPA filters, and operators wear protective clothing. Limitations are set on the materials that can be used to make cleanroom equipment and tools, such as wafer boxes and tweezers, since they are only allowed to generate a minimal amount of particles.
“The use of FFF-based 3-D printing in the cleanroom is limited because of the particles generated during fabrication itself, which depend on numerous factors including filament type, filament color, printing parameters and printer design,” the researchers continue.
The study takes a look at the possibility of using 3D printing for some of the least strenuous applications in the cleanroom environment – those that do not require chemical compatibility. The researchers used two objects – a custom single wafer storage box and a wafer positioner for a metrology system – and tested three 3D printing materials: ABS, PLA and PP, 3D printing them on a LulzBot TAZ 6 3D printer.
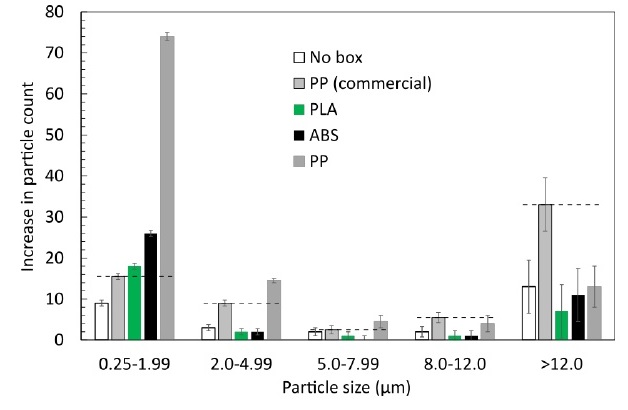
Increase in particle count during 15 days storage in various single wafer boxes. The initial number of particles on all wafers were in the order of 10-20. The dashed lines indicate reference levels set by the commercial PP box, which is commonly used in cleanroom environments. The error bars are determined from the variation in several repeated measurements.
The results of the study show that single wafer boxes 3D printed from PLA and ABS generate as few particles as a commercial equivalent, while slightly more particles were found in the PP box.
“The 3-D wafer positioner seems to cause a negligible particle increase on the manipulated wafer, while abrasion of the mechanical parts generate larger numbers of particles that may disperse in the environment,” the researchers state. “Regular cleaning of those parts is thus recommended, and applicability in a cleanroom environment will depend on the cleanliness constraints.”
Elemental analysis showed that 3D printed objects contained no harmful metal impurities, other than those resulting from colorants, so the researchers recommend that only natural-colored filament be used, especially in applications where metal contamination could be an issue, such as in semiconductor processing.

a) Parts of the positioner modelled in the OpenSCAD software. b) 3-D printed and assembled positioner.
The filaments studied also showed themselves to be resistant to isopropanol and deionized water, which are used for the cleaning of objects in cleanrooms. The researchers conclude that 3D printing is a safe method of creating objects for use in cleanrooms, enabling scientists to take advantage of the cost savings that the technology offers.
Authors of the paper include T.P. Pasanen, G. von Gastrow, I.T.S. Heikkinen, V. Vähänissi, H. Savin and J.M. Pearce.
Discuss this and other 3D printing topics at 3DPrintBoard.com or share your thoughts below.
Metallic Glass Filaments Provides New Metal Printing Process
Researchers at Yale University have just demonstrated a new means of producing metal prints using metallic glass filaments. The technology provides a means of producing metal through processes similar to extrusion. Despite being metal, BMGs (bulk metallic glasses) become far softer upon heating, allowing for easier deposition, similar to that of thermoplastics. Since BMGs have a […]
The post Metallic Glass Filaments Provides New Metal Printing Process appeared first on 3D Printing.