Researchers continue to reach from the 3D realm to the next level, seeking to master the comprehensive fabrication of 4D structures. Now, a team of scientists from Singapore is exploring new ways to create flexible, programmable passive actuators, outlining their findings in the recently published ‘3D Printing of Compliant Passively Actuated 4D Structures.’
For this study, the research team paired compliant mechanisms (CM) with water-responsive chitosan biopolymers. With CM, the scientists were able to take advantage of benefits such as:
- No hysteresis
- Compactness
- Ease of fabrication
- Simplicity
- Light weight
- High reliability
- Frictionless, wear-free motion
CMs are beneficial today in applications such as:
- Implants
- Soft robotics
- Building structures
- Space research
- Micro-engineering
And while there is a long list of ‘pros’, CMs still offer a host of issues researchers, manufacturers, and industrial users must surpass in terms of both design and fabrication. With additive manufacturing being used in CM manufacturing, the goal is to provide the mechanical force required to spur on movement and possible deformation of the compliant part, which may respond to temperature, light, and moisture. Such products are categorized as 4D or ‘smart materials’ as they are able to respond to their environment accordingly.
Materials such as chitosan, an extremely common polymer, have been used more often with 3D printing, in examples like bioprinting neural tissue. Materials bordering on the 4D have been tested and used many times also with soft robotics, reinforced composites, and more.
Initially, a single design was created for the actuator nodes, with a ‘truss-inspired cantilever fitted with hygroscopic chitosan films.’ Chitosan biopolymers allow for the necessary deformation in this project design, as well as many applications today like textiles, cosmetics, agriculture, bioprinting, and more.
As they began working to create four compliant designs, researchers used cotton gauze to strengthen the chitosan, structuring it into thin pieces of film with a specific solution that is filtered, degassed, and then cast into molds. They put the films through another washing and drying cycle and then began experimenting with their designs, on a mission to make strides in achieving suitable and programmable shape deformation. In their prototype, the researchers used an ‘intuitive physical’ concept as they investigated several different CM designs to meet the necessary range of motion in a variety of shapes, layer thickness, and more.
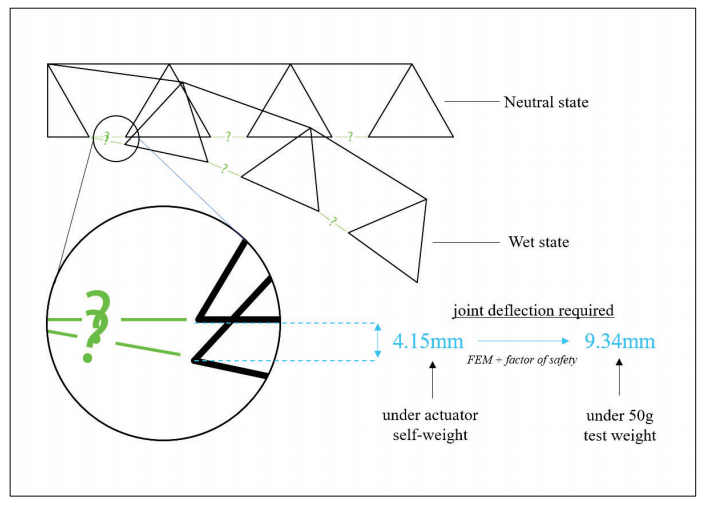
The flexure must be compliant enough to deflect 9.34 mm under the load from a
50gm test weight in order to achieve the targeted shape change
Several ‘springy’ designs were developed to spread the load for each flexure, along with allowing for better control with programmable bending in the system. Strength was evaluated also with a load test, and static non-linear structural FEM analysis.
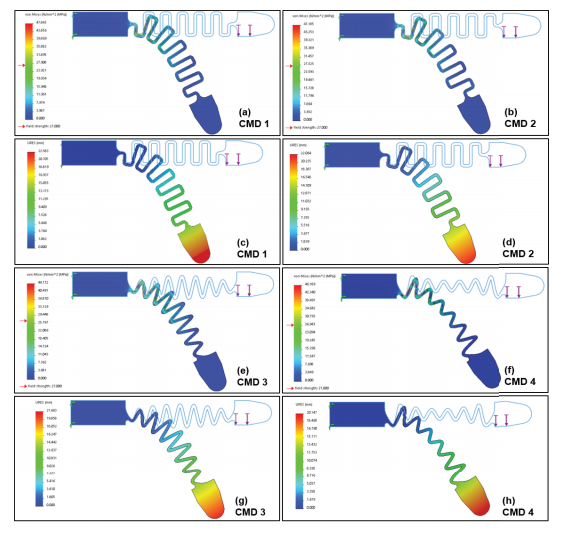
FEA simulation for four different CM designs (a, b, e & f) Maximum stress (c, d, g & h) Maximum deflection
3D printing of the research project’s actuator was performed on a Stratasys Fortus 450mc FDM 3D printer, using ASA—a propriety model material by Stratasys that is similar to ABS. The team spent 4.5 hours printing the part, and then it was placed in a solution to assist in removal of support materials. In testing, the researchers noted good performance from the actuator, with no signs of mechanical failure at all; however, there were still ‘significant variations from the expected results.’
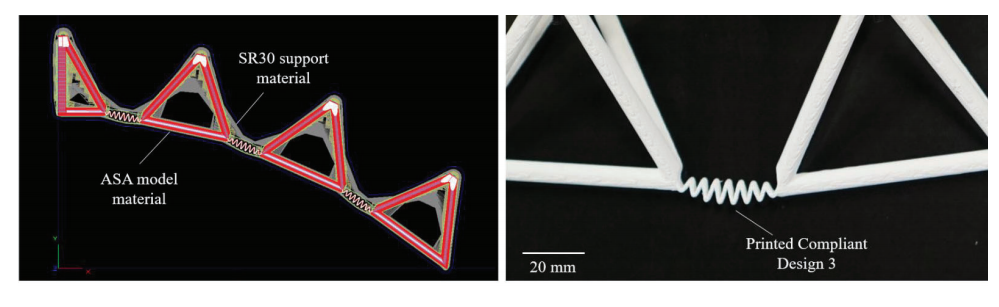
3D printing of the actuator (a) Sliced model of the actuator before printing (b) Print results of CM Design 3
“The average total deformation between the two states of the actuator was calculated to be 71.2mm, measured by changes in height of the cantilevering end of the actuator. This 71.2 mm represents nearly one-third of the total actuator length, which points to the ability of the CM to accommodate a relatively large range of motion. The expected deformation from 2D simulation was 95.6mm, and so evidently the chitosan did not expand to their 12.8 % capacity as expected,” concluded the researchers.
“It is possible that even though the films lose much of their stiffness when saturated, that there was still insufficient driving force to cause significant mechanical strain of the films. One potential workaround would be to implement another tensile element to the assembly that, when added on top of the assembly’s self-weight, could encourage the full elongation of the chitosan films.”

Comparison of (a) Simulated curve of dry and wet state (b) Physical results of dry and wet state curvature
What do you think of this news? Let us know your thoughts! Join the discussion of this and other 3D printing topics at 3DPrintBoard.com.
[Source / Images: ‘3D Printing of Compliant Passively Actuated 4D Structures’]
The post 4D Printing in Singapore: Researchers Pair Compliant Mechanisms with Chitosan Biopolymers appeared first on 3DPrint.com | The Voice of 3D Printing / Additive Manufacturing.
95 Replies to “4D Printing in Singapore: Researchers Pair Compliant Mechanisms with Chitosan Biopolymers”
Comments are closed.