In ‘Rapid Fabrication of High-Performance CaO-Based Integral Ceramic Mold by Stereolithography and Non-Aqueous Gelcasting,’ Chinese researchers from Xi’an Jiaotong University explore 3D printing of better ceramic molds for investment casting. These are extremely important tools in manufacturing for a variety of applications, and mainly for casting structures that are complex and require internal cavities. Most are produced out of silica or alumina with good results, but not when used with active alloys that result in an inferior finish. Here, the authors search for affordable, accessible materials to fabricate ceramic molds that still possess the thermal stability and collapsibility required.
Calcium oxide, or CaO, is the center of focus in this study for a material that would be suitable for the ceramic core of a mold. It offers:
- Reaction-resistance to molten active alloys
- Ease of dissolution
- Similar thermal expansion coefficient to those of superalloys
Susceptibility to water is a major issue with CaO, however, limiting its uses, along with inferior mechanical properties and low density. The researchers experimented with SLA 3D printing and gelcasting, which offers a unique method for creating ceramics via in-situ solidification. The more typical aqueous gelcasting was not a possibility due to hydration issues, but the authors were aware of previous experiments with non-aqueous procedures.
“Tert-butyl alcohol (TBA) has been selected as the solvent due to its low surface tension and high saturation vapor pressure, and the green body can be dried easily and with little shrinkage,” reported the authors.
CaO powder was combined with a pre-mixed solution and then the slurry was poured into a resin mold 3D printed on a SPS600B Rapid Prototyping Machine.
“The green body was subsequently placed into a vacuum freeze-dryer (Beijing Songyuan Huaxing Technology Development Co., Ltd., Beijing, China) with a freezing temperature of −40 °C, shelf temperature of 0 °C, and pressure of 10 Pa for 48 h. Finally, an integral CaO-based ceramic mold was obtained after sintering at 1400 °C for 3 h.,” explained the researchers in their study.
The researchers were able to create a stronger slurry with some adjustment, along with gelation. Cracks were a major concern too, so temperature and heating rate had to be managed accordingly:
“There were no cracks in the CaO-based ceramic crucibles when the heating rate was 0.5 °C/min or 1 °C/min, whereas there were obvious cracks in the crucibles when the heating rate was greater than 1.5 °C/min. Although the ceramic mold did not crack with a heating rate of 0.5 °C /min, the heating rate is too low to facilitate efficient and economical production rates. To balance the quality, efficiency and energy consumption of manufacturing, 1.0 °C/min was considered the most suitable heating rate for pre-sintering the CaO-based ceramic molds,” reported the researchers.
Pre-sintering and sintering were also rigorously managed to control shrinkage, resulting in a low rate of 0.6% and a relatively high high-temperature (1200 °C) bending strength of 8.22 MPa.
“Compared to the injection molding process, the process described in this paper is more efficient for the fabrication of molds with complex structures and cores. The fabrication process of the CaO-based ceramic mold developed in this study is ideal for the rapid manufacturing of active metal parts with complex cavities,” said the researchers. “The process is more suitable for the rapid manufacturing of single-piece or small-batch production than the mass production due to the low efficiency of SLA. The control mechanism and method of near-zero shrinkage and the casting performance of CaO-based mold still need to be considered in further study.”
In a world still held undeniably connected between conventional methods of manufacturing and the mind-blowing progressive, the two commonly intersect—and 3D printing is often used today for making molds so that users can go on to make multiple objects quickly, and often with materials not supported by 3D printing, yet. And although the innovations brought forth by 3D printing are often staggering in their novelty as well as functionality, users around the world have been on a steep learning curve, driven to make one powerful improvement over another.
Find out more about other 3D printed molds such as those used to make elaborate metal architectural structures, glass molds, and PDMS molds for microfluidic designs. What do you think of this news? Let us know your thoughts! Join the discussion of this and other 3D printing topics at 3DPrintBoard.com.
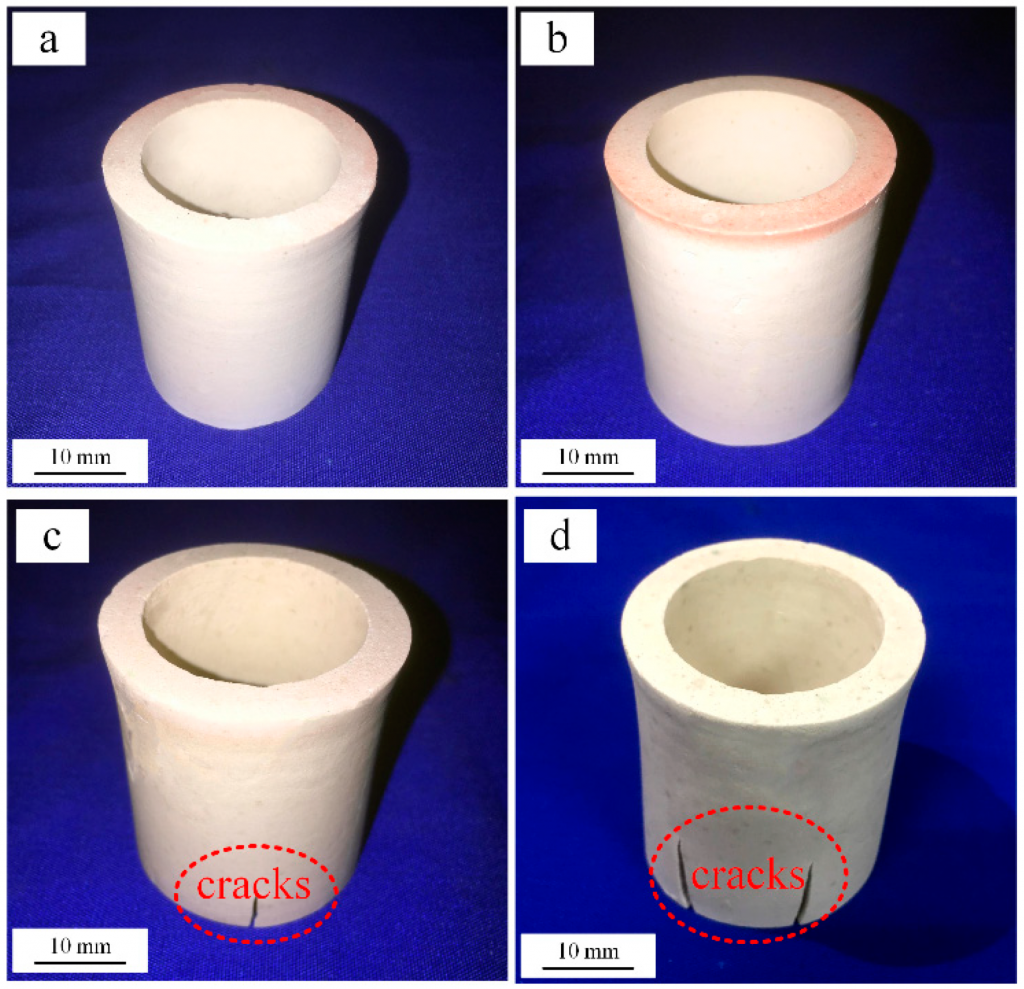
Images of CaO-based parts with different pre-sintering heating rates: (a) 0.5 °C/min, (b) 1.0 °C/min, (c) 1.5 °C/min, and (d) 2.0 °C/min.
[Source / Images: ‘Rapid Fabrication of High-Performance CaO-Based Integral Ceramic Mold by Stereolithography and Non-Aqueous Gelcasting’]
59 Replies to “SLA 3D Printing: Chinese Researchers Create Strong Ceramic Molds with Non-Aqueous Gelcasting”
Comments are closed.