Researchers from the University of Washington are exploring further complexities of material science in metal printing, outlining their findings in the recently published ‘Electron beam additive manufacturing of Ti6A14V: Evolution of powder morphology and part microstructure with powder reuse.’
Concerned with quality for aerospace applications, the authors designed this study to address ‘fundamental issues’ concerning the use of powder bed fusion in additive manufacturing—mainly in re-use. As additive manufacturing continues to increase in popularity for industrial users, the benefits become more apparent—from the ability to create complex and optimized geometries to using significantly fewer materials that are stronger and more durable, yet light in weight. As is generally the case though, challenges exist, such as slow processing times.
“The opportunities for metal AM to be used for manufacturing components with stress-critical applications has caused need for greater understanding of the process,” state the authors.
During the process of EBM powder bed fusion, the characteristics and quality of powder are critical as it is sequentially deposited, sintered, and melted. There are the obvious benefits of reusing powder to cut down on waste of materials, but the effects on mechanical properties of parts are of concern—and an area that the authors point out has previously not been researched fully—and when it has, reuse cycles have involved ‘relatively low exposure time of the powder during the build process.’
“There are many concerns that remain to be addressed in powder reuse for metal AM,” state the researchers, pointing out the necessity for an analysis of part microstructure.
Researching powder reuse in EBM AM of Ti6Al4V, the authors performed 30 build cycles. They also investigated the following:
- Transformations in powder chemistry
- Particle size distribution with reuse
- Effects on the built metal part
“The novelty of this investigation regarding powder reuse is in the large number of reuse cycles achieved for EBM AM, the extensive evaluation of powder that was performed, and the complimentary evaluation of the part microstructure,” stated the authors.

Details of the manufactured specimens. (a) Schematic diagram of the parts and their distribution in each build. Parts in each build include (A) six vertical and (B) six horizontal oriented flat tensile specimen (ASTM E08M), a (C) vertical and horizontal oriented staircase, a (D) small cylinder, and (E) a cylindrical step pyramid. (b) geometry of the staircase specimens and (c) pyramid specimen showing relevant dimensions and locations of repeated microstructural analysis as highlighted by the squares.
Grade 5 Titanium alloy (Ti6Al4V) was used, with the 30 builds performed over six months on an ARCAM A2X Electron Beam AM system, from ‘b1 for the first build performed with 50 kg of virgin powder and subsequently up to b30 for the final build.’

Micrograph of the “as-built” microstructure. (a) prior β grains with boundaries outlined with red arrows. (b) The line intercept method employed to determine the prior β grain columnar width. (c) Micrograph of as-built microstructure with highlighted β ribs and α laths.
During the study and ongoing builds, the research team noted that particles did change in size, and both surface texture and morphology changed also as the powder was reused.
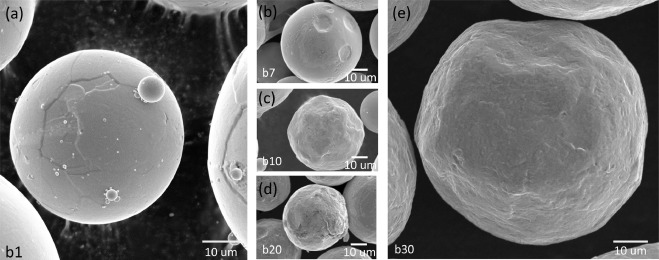
Progression of powder size and morphology through the reuse process. (a) In virgin powder (b1), particle surfaces are relatively smooth and they have high sphericity. There is numerous tiny particles that agglomerate or adhere to the surface of larger particles. Representative views of powder in b7, b10, and b20 in (b)–(d), respectively, show the progression of particle surface damage and the absence of tiny particles. In b30 (e), the particles are irregular with some exhibiting major deformation and damage.

Examples of damaged particles in powder of b1, b14, and b30. Specimen examples of (a) fractured, (b) agglomerated/fused, and (c) melted/irregular particles are shown, respectively. In general, damaged particle of these types were found in the powder of all builds evaluated by SEM.
Staircase and pyramid part samples were used in this study to examine how powder reuse affected the printed Ti6Al4V microstructure. Both samples were cross-sectioned and mounted during evaluation, polished, then etched by immersion.
“In comparing responses for the two geometries, the primary difference in microstructure between the pyramids and staircases is the broader spread of alpha volume and lath thickness in the pyramid, along with the increase in alpha lath thickness with powder reuse,” stated the researchers in discussion.
“One of the most marked changes in powder with reuse was the increase in surface deformation to the particles and physical damage. The particles changed shape with reuse cycles from spherical geometry to increasingly deformed with surface dimples and irregular shape,” concluded the researchers. “This aspect of the powder degradation appears to result from the mechanical aspects of the recycling and part extraction process. In addition, there was an increase in fractured particles, partially fused particles and recast particles with powder reuse.”
[Source / Images – ‘Electron beam additive manufacturing of Ti6A14V: Evolution of powder morphology and part microstructure with powder reuse’]
The post University of Washington Researchers Analyze Effects of Powder Reuse on 3D printed Metal Parts appeared first on 3DPrint.com | The Voice of 3D Printing / Additive Manufacturing.