Authors Sara Coppola, Giuseppe Nasti, Veronica Vespini, and Pietro Ferraro explore a new technique for 3D printing with biocompatible materials, outlined in ‘Layered 3D Printing by Tethered Pyro-Electrospinning.’ Motivated to overcome current challenges in the fabrication of fibers on both the micro- and nanoscale, the researchers offer a novel 3D printing method with the use of moderate temperatures resulting in both accuracy and flexibility.
Fibers today can be 3D printed for a variety of applications like wearables, custom biomedical devices, drug-delivery systems, bioprinted scaffolds, and more. While electrospinning is already a popular method for creating fibers, pyro-electrohydrodynamic (pyro-EHD) printing can be used for creating polymers fibers while overcoming typical EHD processes which are governed by nozzle size.
This study demonstrates the first use of pyro-EHD methods for creating biodegradable and biocompatible polymers with a variety of geometries and micro-architectures to include:
- Wall
- Square
- Triangle
- Hybrid structures
Materials used for samples consisted of Poly(lactic-co-glycolic acid) PLGA and dimethyl carbonate, with fluorochrome as an additive to the polymer for use as a model drug. In creating the polymeric fibers, the research team used tethered pyro-electrospinning, activated as a drop of the solution was used as a reservoir and then placed under the LN crystal plate.
“The reservoir drop was directly pipetted over a hydrophobic micropillar made in Polydimethylsiloxane (PDMS) and placed over a commercial microscope glass slide,” explained the researchers. “Under the activation of the TPES process, the droplet started to deform, creating an elongated tip from which fibers were drawn. The target used for the collection was placed in front of the drop and removed at the end of the over-printing procedure.”
Over-printing occurs as an ‘intense pyroelectric field’ emerges from the LN crystal, according to the right temperature. The researchers used the following equipment while engaged in pyro 3D printing:
- Reservoir solution drop
- Pyroelectric crystal
- Thermal control system
- Programmable stage motion
- Glass target holder
- Manual micro-stages with axis control
Once the pyroelectric material reaches a temperature of about 80°, a high electric field is created. High voltage is then charged between the crystal and the plate supporting the drop, with ions gathering within the printing solution—forming chargers.
“The charges would bring an electrostatic force to deform the drop’s meniscus to form a conical shape (Taylor cone),” explain the researchers. “When the electrostatic force will overcome the surface tension at the Taylor cone, a jet would be injected from the meniscus onto the receiving substrate.
“The reservoir droplet is sited in front of the active crystal at a distance h < 1 mm. The selected distance allows preventing the jetting from buckling as it hits the target. In this way, the bending instability and splitting of the charged jet are overcome.”

Outline of the set-up for layered 3D printing: the reservoir drop is sited under the LN crystal heated by a thermal control system. During the experiment, real-time visualization was ensured in order to control at the same time the jetting process and the target position. For the fabrication of layered architecture, the target was moved along the x,y direction. In the top-view the pink trails and the arrows indicate the direction of movement.
Jet diameter relies on:
- Surface tension
- Flow rate
- Dielectric constant
- Electric current
Plotting varied due to the impacts of ink properties, printing parameters, and temperature.
Fiber characteristics were adjusted during the TPES printing process, with fibers placed on the substrate and microstructures ‘obtained by superimposition.’ The research team noted that three parameters affected fiber diameters, with a temperature of 110°C activating the pyro-electric effect.
“The resulting printed fibers had a diameter (d) ranging between 10 μm < < 30 μm. Controlling these parameters could be possible to produce fiber of about 1 μm diameter or even less, as demonstrated in case of TPES,” stated the researchers.

Schematic outline of three-dimensional architectures: (a) a single wall freestanding along the direction was constructed by overlay, the blue arrows indicate the direction of printing, (b) a single wall was constructed crossing a matrix of single fibers, creating a sort of square profile where only one side was obtained by superimposition, (c) a cubic architecture was constructed side by side, starting from the fabrication of the first wall (side ) all the adjacent sides were completed in a clockwise direction, and (d, e) cubic and triangular architecture were obtained by overlay of the complete profile, starting from the first track, the same profile was overwritten. The blue arrows indicated the direction of printing.
Pattern models, pre-designed for the study, manipulated motion during each stage, allowing for the layers to be fabricated. A high-resolution stage was necessary for the proper regulation of features and patterns.
The experimental portion of the study involved doping their PLGA/DMC solution with fluorochrome. Both PLGA and DMC are highly dissolvable, but also biodegradable and attractive for use in this study. Microstructures were fabricated from the initial single wall, serving as a ‘building block’ for future layers of polymeric fibers.
After printing simple walls, the researchers moved on to more complex geometries such as a polymeric grid and a square, with all sides comprised of five layers.

(a) Schematic outline of the experiment. (b) Streomicroscope image of a single wall crossing a matrix of single fibers at the bottom. (c) Close up of the crossing and focus on a crossing point making evident the good control in superimposition (d).
“Following the same procedure for the realization of a regular three-dimensional microstructures we tested a triangular geometry where the angles between the adjacent side are acute ~30°. The construction of the architecture by superimposing the complete profile three times resulted in a good spatial resolution and vertical finishing,” stated the researchers.
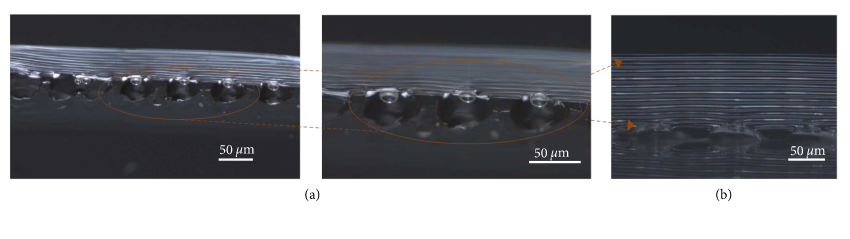
(a) Hybrid microstructure made of hemispherical drops and multi-layered fibers. The drops were used as pillars for the construction of a free-standing wall. (b, c) Stereomicroscope image and close up of the sustaining pillars and of the overprinted fibers.
“ … starting from the fabrication of elementary geometry (wall, cubic, and triangular microstructures) this work represents the base for the design of more complex microarchitectures. The fabrication process is described in detail; the fabricated microstructures have been characterized, focusing on the use of composite material and, in particular, of biocompatible and biodegradable biomaterials,” concluded the researchers. “Taken into account that there is a growing demand for novel products and devices such as encapsulation systems, it is easy to imagine that the exploitation of different additive manufacturing approaches could find use in regenerative medicine with a strong interest in the development of in vivo bio-incubators that better replicate the tissue environment.”
3D printed microstructures and architectures continue to be a source of innovation via researchers around the world, involving research for new drug delivery systems, optics, tissue repair, and more.
What do you think of this news? Let us know your thoughts! Join the discussion of this and other 3D printing topics at 3DPrintBoard.com.
[Source / Images: ‘Layered 3D Printing by Tethered Pyro-Electrospinning’]
The post A New 3D Printing Method: Tethered Pyro-Electrospinning for 3D Printed Microstructures appeared first on 3DPrint.com | The Voice of 3D Printing / Additive Manufacturing.
31 Replies to “A New 3D Printing Method: Tethered Pyro-Electrospinning for 3D Printed Microstructures”
Comments are closed.