
Custom laser powder bed fusion test setup for producing single track samples in an argon flow and capturing high speed image data of the process.
From bioprinting blood vessels and using 3D printing to control reactive materials to 3D printing nanoporous gold and researching metal 3D printing flaws, the scientists at Lawrence Livermore National Laboratory (LLNL) are well known for their impressive work with 3D printing materials. Recently, a group of LLNL researchers explored the use of spatial laser modulation in enhancing the processability and properties of 3D printing metals. The team created a custom laser powder bed fusion (LPBF) test bed, which can produce single tracks of steel 316L under various conditions.
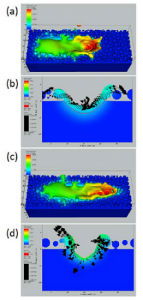
Top and transversal cross-sectional views of simulated melt-track formation by the Gaussian (a, b) and longitudinal elliptical (c, d) beams, where laser scanning occurs in the positive x-direction.
The alloys used most often for metal 3D printing, like 316L stainless steel, titanium alloys like Ti–6Al–4V, Inconel 718/625 superalloys, and aluminum alloys such as Al–Cu–Mg–Sc–Si, are more developed for standard manufacturing than they are for AM processing; reasons for this include unsuitable materials feedstocks, little control over local thermal histories that drive microstructure control, and deficient predictive capabilities due to limited data from in situ process monitoring.
In addition, while metal LPBF 3D printing has a lot of potential for a wide variety of applications, it lacks the degree of control that’s necessary to produce parts that can meet exacting, performance-driven criteria. In order to continue driving 3D printing from a rapid prototyping mindset to rapid manufacturing, it’s important to have in-depth knowledge of the AM process and the structures it can create. To do this, the LLNL researchers are working to develop a new science-based AM design strategy that can control thermal history by using tailored and simulation-driven light sources.
M.J. Matthews, T.T. Roehling, S.A. Khairallah, G. Guss, S.Q. Wu, M.F. Crumb, J.D. Roehling, and J.T. McKeown with LLNL recently published a paper, titled “Spatial modulation of laser sources for microstructural control of additively manufactured metals,” where they demonstrate how beam ellipticity can be used for microstructural control during LPBF 3D printing.
The abstract reads, “In this work, we explore spatial laser modulation to enhance the properties and processability of AM metals. Experiments are carried out with the goals of demonstrating control of the columnar-to-equiaxed transition, identify methods to reduce surface roughness, and extend processing windows for AM alloys. Results show that beam modulation provides site-specific microstructural control, and these results are interpreted using finite element modeling of the melt pool dynamics and thermal profiles.”
The team used simple beam shaping optical elements which could, in theory, be implemented on a commercial AM system someday.
“Thus, through engineering of the thermal gradients with such optics, it may be possible to control equiaxed or columnar grains at specified locations by modulating beam shape during a build,” the researchers wrote.
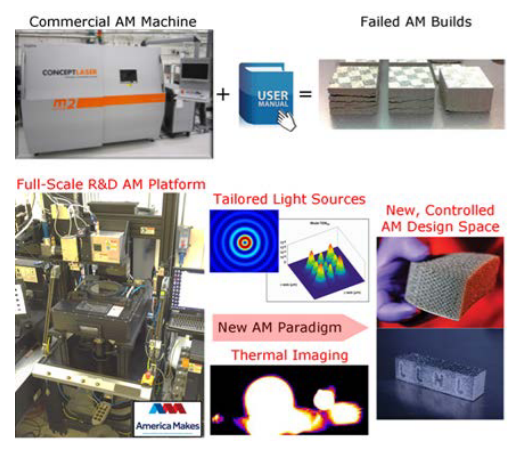
Conceptual framework for tuning material properties in AM using tailored light sources like shaped beams.
316L stainless steel powder from Concept Laser on 316L stainless steel substrates was used during the single-track laser melting experiments. In their LPBF testbed, the team used a 50 mm FL lens to make rays of light from of a 600 W fiber laser parallel. Using LLNL’s ALE3D numerical simulation software tool, the researchers modeled the actual particle size distribution and random particle packing, before using a laser ray tracing algorithm to simulate laser interaction with the actual powder bed.
“The three-dimensional model was addressed using a hybrid finite element and finite volume formulation on an unstructured grid,” the researchers wrote. Simulations were run using each beam shape at Size S for P = 550 W. To conserve computational time, the scan velocity was set at 1800 mm/s, resulting in an energy density of 61 J/mm3. This energy density is slightly lower than the minimum value used in the experiments (80 J/mm3).”
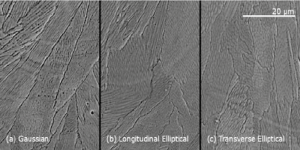
Microstructure cross-sections as a function of beam shape: (a) Gaussian, (b) longitudinal elliptical and (c) transverse elliptical.
Using LLNL’s ALE3D code to model laser-model interactions made it possible to investigate beam shape effects on track macro- and microstructures. The researchers determined that “equiaxed solidification was favored at lower laser powers,” independently of beam ellipticity or size; this was observed particularly when substrate penetration by the melt was poor or even absent.
The concentration of columnar grains generally increases when the power and scan speed goes up as well, and the parameter space, “over which equiaxed or mixed equiaxed-columnar microstructures” were made,” was larger for elliptical beams than it was for Gaussian ones. This shows that it it is possible to achieve site-specific microstructural control by varying the beam ellipticity. Additionally, even more complex microstructures are possible with full builds that use alternate beam shapes.
“The effects of Gaussian and elliptical laser intensity profiles on single-track microstructures were investigated. Beam ellipticity demonstrated a strong effect on solidification microstructure. The elliptical intensity profiles produced equiaxed or mixed equiaxed-columnar grains over a much larger parameter space than the circular profiles when conduction-mode laser heating occurred. This indicates that grain morphology can be tailored by varying beam intensity spatial profile while maintaining constant laser power and scan speed,” the researchers concluded.
Because the research showed that it’s possible to locally tune microstructures, users can now engineer site-specific properties right into 3D printed parts, which ultimately means more design flexibility.
Discuss this research and other 3D printing topics at 3DPrintBoard.com or share your thoughts below.
113 Replies to “LLNL Researchers Use Laser Beam Shaping to Enhance Properties During Metal 3D Printing”
Comments are closed.