
Microscopic photos of top and side views of printing results with a 0.38 mm wide extrusion path: (a) without versus (b) with overlapping by 0.36 mm respectively. Overlapping extrusion paths exhibit over-extrusion of material at the overlapping region, which results in unwanted blobs on the surface of the print.
Plenty of research has been completed in regards to FDM (extrusion) 3D printing, such as how to improve part quality and how to reliably fabricate functionally graded materials (FGM). The latter is what a collaborative team of researchers from Ultimaker, the Delft University of Technology (TU Delft), and the Chinese University of Hong Kong are focusing on in their new research project.
The team – made up of researchers Tim Kuipers, Jun Wu Charlie, and C.L. Wang – recently published a paper, titled “CrossFill: Foam Structures with Graded Density for Continuous Material Extrusion,” which will be presented at this year’s Symposium for Solid and Physical Modeling.
“In our latest paper we present a type of microstructure which can be printed using continuous extrusion so that we can generate infill structures which follow a user specified density field to be printed reliably by standard desktop FDM printers,” Kuipers, a Software Engineer and Researcher for Ultimaker, wrote in an email.
“This is the first algorithm in the world which is able to generate spatially graded microstructures while adhering to continuous extrusion in order to ensure printing reliability.”
Because 3D printing offers such flexible fabrication, many people want to design structures with spatially graded material properties. But, it’s hard to achieve good print quality when using FDM technology to 3D print FGM, since these sorts of infill structures feature complex geometry. In terms of making foam structures with graded density using FDM, the researchers knew they needed to develop a method to generate “infill structures according to a user-specific density distribution.”
The abstract reads, “In this paper, we propose a new type of density graded structure that is particularly designed for 3D printing systems based on filament extrusion. In order to ensure high-quality fabrication results, extrusion-based 3D printing requires not only that the structures are self-supporting, but also that extrusion toolpaths are continuous and free of self-overlap. The structure proposed in this paper, called CrossFill, complies with these requirements. In particular, CrossFill is a self-supporting foam structure, for which each layer is fabricated by a single, continuous and overlap-free path of material extrusion. Our method for generating CrossFill is based on a space-filling surface that employs spatially varying subdivision levels. Dithering of the subdivision levels is performed to accurately reproduce a prescribed density distribution.”
Their method – a novel type of FDM printable foam structure – offers a way to refine the structure to match a prescribed density distribution, and provides a novel self-supporting, space-filling surface to support spatially graded density, as well as an algorithm that can merge an infill structure’s toolpath with the model’s boundary for continuity. This space-filling infill surface is called CrossFill, as the toolpath resembles crosses.
“Each layer of CrossFill is a space-filling curve that can be continuously extruded along a single overlap-free toolpath,” the researchers wrote. “The space-filling surface consists of surface patches which are embedded in prism-shaped cells, which can be adaptively subdivided to match the user-specified density distribution. The adaptive subdivision level results in graded mechanical properties throughout the foam structure. Our method consists of a step to determine a lower bound for the subdivision levels at each location and a dithering step to refine the local average densities, so that we can generate CrossFill that closely matches the required density distribution. A simple and effective algorithm is developed to merge a space-filling curve of CrossFill of a layer into the closed polygonal areas sliced from the input model. Physical printing tests have been conducted to verify the performance of the CrossFill structures.”
The researchers say that the user prescribes density distribution, and can use CrossFill and its space-filling surfaces, with continuous cross sections, to “reliably reproduce the distribution using extrusion-based printing.” CrossFill surfaces are built by using subdivision rules on prism-shaped cells, each of which contains a surface patch that’s “sliced into a line segment on each layer to be a segment” of the toolpath, which will be made with a constant width; cell size determines the density.
“By adaptively applying the subdivision rules to the prism cells, we create a subdivision structure of cells with a density distribution that closely matches a user-specified input,” the team wrote. “Continuity of the space-filling surface across adjacent cells with different subdivision levels – both horizontally and vertically – is ensured by the subdivision rules and by post-processing of the surface patches in neighboring cells.”
The subdivision system distinguishes an H-prism, which is built by cutting a cube in half vertically along a diagonal of the horizontal faces, and a Q-prism, generated by spitting a cube into quarters along the faces’ diagonals. To learn more about this system and the team’s algorithms, check out the paper in its entirety.
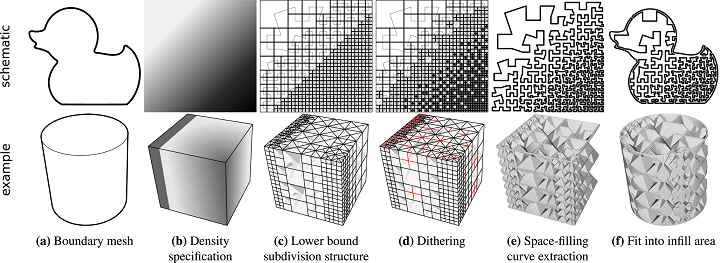
Schematic overview of our method. The top row shows a 2D analogue of our method for clear visualization. The prism-shaped cells in the bottom row are visualized as semi-opaque solids to keep the visualization uncluttered. Red lines in the bottom row highlight the local subdivisions performed in the dithering phase.
The researchers also explained the method’s toolpath generation in their paper, starting with how to slice the infill structure into a continuous 2D polygonal curve for each layer of the object, which is followed by fitting a layer’s curve “into the region of an input 3D model.”
Experiments measuring features like accuracy, computation time, and elastic behavior were completed on an Intel Core i7-7500U CPU @ 2.70 GHz, using test structures 3D printed out of white TPU 95A on Ultimaker 3 systems with the default Cura 4.0 profile of 0.1 mm layer thickness. The team also discussed various applications for CrossFill, such as imaging phantoms for the medical field or cushions and packaging.
“The study of experimental tests shows that CrossFill acts very much like a foam although future work needs to be conducted to further explore the mapping between density and other material properties,” the researchers concluded. “Another line of research is to further enhance the dithering technique, e.g. changing the weighing scheme of error diffusion.”
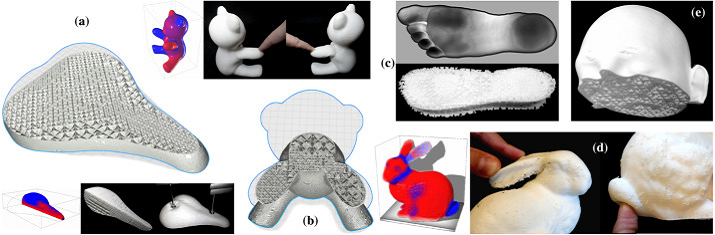
CrossFill applications. (a) Bicycle saddle with a density specification. A weight of 33 N is added on various locations to show the different response of different density infill. (b) Teddy bear with a density specification. (c) Shoe sole with densities based on a pressure map of a foot. (d) Stanford bunny painted with a density specification. (e) Medical phantom with an example density distribution for calibrating an MRI scanning procedure.
The team’s open source implementation is available here on GitHub. To learn more, check out their video below:
Discuss this story, and other 3D printing topics, at 3DPrintBoard.com or share your thoughts below.
152 Replies to “Collaborative Research Team Develops Density-Graded Structure for Extrusion 3D Printing of Functionally Graded Materials”
Comments are closed.